Introduction: What is Steel!!
Steel, an essential material in modern infrastructure and industries, is an alloy consisting primarily of iron and carbon. This composition, with carbon content up to a maximum of 1.5%, imparts desirable properties such as hardness and strength to the steel. Additionally, other elements like silicon, sulphur, phosphorus, and manganese are often present in varying amounts to further enhance specific properties. In this blog post, we will delve deeper into the world of steel, exploring its different types based on carbon content, grades, and the effects of various impurities. Furthermore, we will discuss the physical and mechanical properties of steel that make it a versatile and vital material in numerous applications.
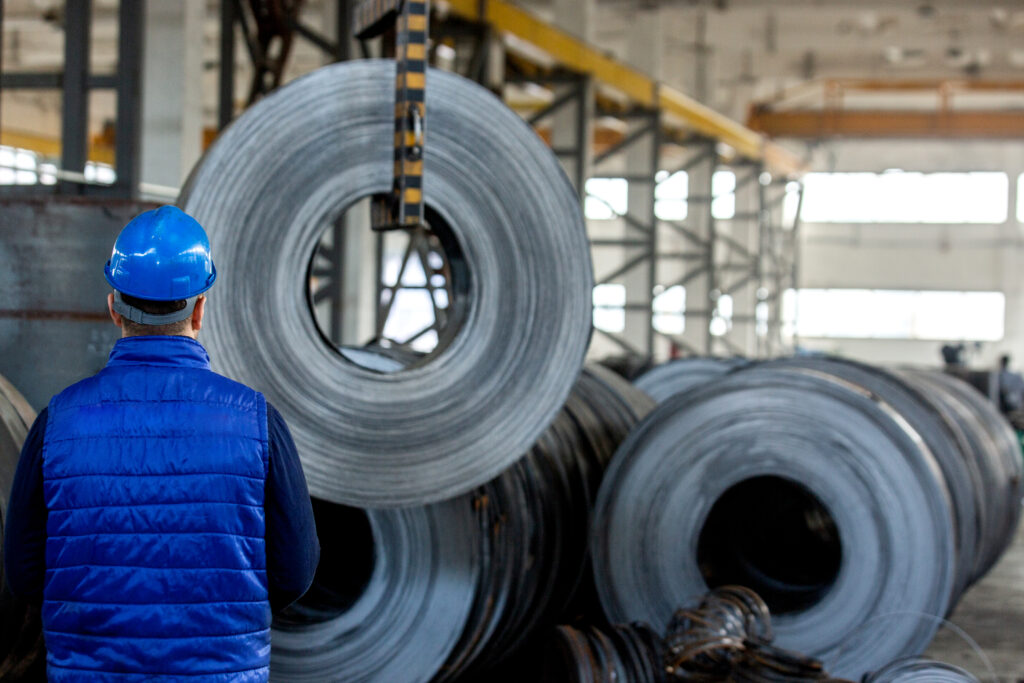
Table of Contents
1. Composition and Types of Steel:-
Steel is classified into different types based on its carbon content, each with unique characteristics and applications:
- Dead Mild Steel: This type contains up to 0.15% carbon, making it exceptionally soft and malleable.
- Low Carbon or Mild Steel: With carbon content ranging from 0.15% to 0.45%, this type strikes a balance between ductility and strength.
- Medium Carbon Steel: Carbon content between 0.45% and 0.8% characterizes this type, providing increased strength and hardness.
- High Carbon Steel: Featuring carbon content from 0.8% to 1.5%, this type exhibits superior hardness and is often utilized in applications that require extreme durability.
2. Grades and Applications of Steel:-
Steel grades are designated based on their mechanical properties and intended usage. In India, the IS (Indian Standard) system categorizes steel grades using symbols such as ‘Fe‘ or ‘Fe E‘ followed by a numerical value denoting minimum tensile strength or yield stress. For example, ‘Fe 290’ signifies steel with a minimum tensile strength of 290 N/mm².
In accordance with the Indian standard IS-2062, steel is classified into nine different grades: E250, E275, E300, E350, E410, E450, E550, E600, and E650. Within the range of grades E250 to E410, there are four sub-qualities available: A, BR, B0, and C. For grades E450 to E650, there are two sub-qualities: A and BR.
Each sub-quality represents specific requirements for impact testing and de-oxidation methods, as outlined below:
- Sub-quality A: Impact testing is not required, and the steel can be either semi-killed or killed during the manufacturing process.
- Sub-quality BR: Impact testing is optional, and if required, it is conducted at room temperature. The steel can be either semi-killed or killed.
- Sub-quality B0: Impact testing is mandatory at 0°C, and the steel can be either semi-killed or killed.
- Sub-quality C: Impact testing is mandatory at -20°C and the steel must be killed during production.
The grades E250 to E300 are classified as low-tensile steels suitable for general structures. Grades E350 to E450 fall under the category of medium-tensile structural steels. Finally, grades E550 to E650 offer higher tensile strength and are classified as high-tensile steels.
These grade classifications and sub-qualities provide valuable information for selecting the appropriate steel grade based on the required mechanical properties, impact resistance, and de-oxidation characteristics.
3. Effects of Impurities on Steel:
Impurities in steel, such as silicon, sulphur, manganese, and phosphorus, can impact its properties. Here are some notable effects:
- Silicon: Typically present in the range of 0.05% to 0.30%, silicon is added to low-carbon steels to prevent porosity. It removes gases and oxides, improving toughness and hardness.
- Sulphur: Found as iron sulphide or manganese sulphide, sulphur can cause red shortness in steel due to its low melting point. Manganese sulphide has a lesser effect, making it more favorable in steel production.
- Manganese: This element serves as a deoxidizing and purifying agent in steel, enhancing ductility and bending qualities in low-carbon steels. In high-speed steels, manganese toughens the metal and raises its critical temperature.
- Vanadium: Adding a small amount of vanadium (less than 0.2%) results in increased tensile strength and elastic limit without sacrificing ductility in low and medium-carbon steels. Chrome-vanadium steel exhibits excellent properties and is commonly used in various applications.
- Cobalt: Cobalt improves red hardness at high temperatures and increases hardness, strength, and magnetic properties in steel for magnets. However, it can lead to decarburization during heat treatment.
- Molybdenum: Often combined with chromium and manganese, molybdenum steel possesses enhanced tensile strength, making it suitable for applications like aircraft fuselages and automobile parts.
- Nickel: Nickel is commonly added to steel to enhance its corrosion resistance. It increases the steel’s resistance to various corrosive environments, including acids, alkalis, and seawater. Nickel also improves the toughness and strength of steel, making it suitable for applications in industries such as aerospace, chemical, and marine.
- Chromium: Chromium is a crucial alloying element in stainless steel. It provides excellent corrosion resistance and oxidation resistance to steel. The formation of a passive oxide layer on the surface of the steel, known as chromium oxide, helps protect the underlying metal from further corrosion. Additionally, chromium improves hardness, wear resistance, and high-temperature strength in steel.
- Phosphorus: Phosphorus is commonly present in steel as an impurity and is typically undesirable. High phosphorus content can lead to brittleness in steel, reducing its toughness and impact resistance. Therefore, phosphorus is usually controlled at low levels during steel production to ensure good mechanical properties.
- Aluminium: Aluminium is often added to steel as a deoxidizer and grain refiner. It helps remove oxygen from the molten steel during the refining process and prevents the formation of oxide inclusions. Aluminium also refines the grain structure of steel, improving its mechanical properties, such as strength and toughness.
- Copper: Copper is primarily added to steel as a strengthening agent. It enhances the steel’s mechanical properties, including strength, hardness, and resistance to wear. Copper can also improve the steel’s corrosion resistance, particularly in acidic environments. However, excessive copper content can lead to reduced ductility and may negatively affect weldability.
- Titanium: Titanium is added to steel primarily for its grain-refining properties. It helps control the grain size and shape during solidification, resulting in improved mechanical properties, such as strength and toughness. Titanium can also enhance the steel’s resistance to corrosion, particularly in acidic and chloride-rich environments.
- Vanadium: Vanadium is commonly used as an alloying element in steel to improve its strength, toughness, and wear resistance. It forms very hard carbides, which contribute to the hardness and wear resistance of steel. Vanadium also refines the grain structure of steel, leading to improved toughness and impact resistance.
It is important to note that the effects of impurities on steel can vary depending on their concentration, the specific type of steel, and the intended application. Steel manufacturers carefully control the composition of steel to achieve desired properties and minimize the negative impacts of impurities.
4. CE(Carbon Equivalent):-
CE stands for Carbon Equivalent, which is a value used to assess the weldability and hardenability of steel. It is a calculation that takes into account the combined effects of various alloying elements on the steel’s behavior during welding and heat treatment.
The Carbon Equivalent (CE) formula varies depending on the steel standard or specification being used. However, the general concept is to evaluate the equivalent carbon content in the steel, considering the influence of other alloying elements.
The CE value helps determine the risk of several issues that can arise during welding and heat treatment, such as cracking, distortion, and the formation of undesirable microstructures. By assessing the carbon equivalent, welders and engineers can make informed decisions regarding welding parameters, preheating, post-weld heat treatment, and material selection.
The effect of carbon equivalent on steel can be summarized as follows:
- Weldability: High carbon equivalent values indicate a higher risk of weld cracking, particularly in heat-affected zones. It is because high carbon equivalent levels are associated with increased hardenability, which can lead to the formation of brittle microstructures during rapid cooling. By managing the carbon equivalent, weldability issues can be minimized, and proper welding techniques can be employed to avoid cracking.
- Hardenability: The carbon equivalent also provides an estimation of the steel’s hardenability, which is its ability to achieve a hardened microstructure through heat treatment. Higher carbon equivalent values indicate increased hardenability, meaning the steel has a greater tendency to form martensite during quenching. This information is crucial for selecting appropriate heat treatment processes to achieve the desired mechanical properties.
It is important to note that different steel standards and specifications may use different formulas to calculate the carbon equivalent. Each formula considers different alloying elements and their respective influence on the steel’s behavior. Therefore, it is essential to consult the relevant standard or specification to determine the specific carbon equivalent calculation and its corresponding effects on the steel.
According to the Indian Standard, the CE formula is:-

Steel is a ferrous metal that is produced as a by-product of iron. It is primarily composed of iron, making it a ferrous metal. Steel possesses various physical and mechanical properties, which contribute to its wide range of applications.
In terms of physical properties, steel has a density of 7850 kg/m³, indicating its relatively high mass per unit volume. It also has a melting point of 1510°C, making it suitable for high-temperature applications. Additionally, steel exhibits a thermal conductivity of 50.2 W/m·°C, allowing it to efficiently conduct heat.
5. Mechanical Properties:-
Steel’s mechanical properties are crucial in determining its performance in various applications. Here is an elaboration of some of these properties:
- Strength: Steel is renowned for its exceptional strength, which enables it to withstand heavy loads and resist deformation. This property makes it suitable for structural components in buildings, bridges, and machinery.
- Stiffness: Steel possesses high stiffness, meaning it can resist deformation when subjected to external forces. Its stiffness allows it to maintain its shape and structural integrity under load, ensuring stability in various applications.
- Elasticity: Steel exhibits elasticity, meaning it can deform under stress but return to its original shape once the stress is removed. This property is advantageous in structures subjected to dynamic loads or where flexibility is required.
- Plasticity: Steel also demonstrates plasticity, enabling it to undergo permanent deformation without fracturing. This property is utilized in processes such as metal forming and shaping.
- Ductility: Steel is highly ductile, meaning it can be stretched or drawn into thin wires without breaking. Its ductility facilitates the production of wires, cables, and other applications that require malleability.
- Brittleness: Although steel is generally not considered brittle, certain types of steel can exhibit brittle behavior under specific conditions. Brittle materials tend to fracture without significant deformation when subjected to stress.
- Malleability: Steel exhibits good malleability, allowing it to be easily shaped or rolled into desired forms without breaking. This property is valuable in manufacturing processes such as forging and rolling.
- Toughness: Steel possesses toughness, which refers to its ability to absorb energy without fracturing. This property makes it resistant to impacts and shock loads, ensuring durability in various applications.
- Hardness: Steel can exhibit different levels of hardness, depending on its composition and heat treatment. Hardness refers to a material’s resistance to indentation or scratching and is essential for applications requiring wear resistance, such as cutting tools.
- Fatigue: Steel’s fatigue resistance is crucial in applications subjected to cyclic loading. It refers to its ability to withstand repeated stress cycles without failure.
- Creep: At elevated temperatures and under constant stress, steel can experience creep, which is the gradual deformation over time. Creep resistance is essential in applications where materials are exposed to high temperatures for extended periods.
These mechanical properties collectively contribute to steel’s versatility, making it an indispensable material in industries such as construction, automotive, aerospace, and manufacturing.
Conclusion:
Steel, an alloy of iron and carbon, is a versatile material that forms the backbone of modern infrastructure and industries. Its composition, grades, and the inclusion of specific elements impact its properties, allowing for a wide range of applications. From structural components to machinery parts, steel’s physical and mechanical properties make it a crucial material in various sectors. Understanding the composition and properties of steel enables engineers and manufacturers to select the appropriate grade for their specific needs, ensuring the durability and performance of their products.
The process of making steel can be viewed here.
I like this weblog it’s a master piece! Glad I found this ohttps://69v.topn google.Raise blog range